Posting all of these on a blog thing means the newer stuff appears on top, and the older stuff below. If you're new here you should start reading from the last post upwards.
I actually started putting it all up after it was done, so disregard all the post dates, although they are all in order. I believe the 1st post should be about 6 months ago, didn't seem like a long time ago now.
If you have something you want to say, you can leave comments or leave messages in the box on the right.
I hope this helps someone, it has certainly been fun for me (and I can now claim I can pull the engine in 45mins and transmission within the next hour).
Monday, November 30, 2009
Sunday, April 12, 2009
Mwhahaha Look at this
Alright! Look at what I got, and am messing with the past couple of days.
o.O It's the throttle body from the German L-jetronic setup. Here's the rest of the parts porn.
The ECU (more specifically this is the housing).
Manifold and injectors mounted, I have to test these out the car somehow, figure it out later.
Throttle cable linkage, there's a ball joint thingy on the throttle body that links to the right end.
AFM, I've taken this apart, haven't touched anything yet, as you can see it's missing the idle screw plug, so someone must've messed with it in the past. AFM porn to come later.
The thermo-time switch, I think mine's wonky, it won't close when I heat the sensor end. Doesn't really matter to me, I'm planning to leave the cold start valve out, Singapore doesn't go below 20deg anyways, I'm thinking the enrichment from a cold head temp sensor is enough, I might be wrong.
The build quality on the ECU is absolutely insane, quality WIMA capacitors all over. The solder used has a high silver content, it still looks shiny after all these years. Everybit that can vibrate, has a little damper underneath it. Transistors have little leg isolators under them, the heatsinked, I'm guessing mil-spec opamps, components have gold leads on them. Pretty insane.

For some weird reason my ECU doesn't seem to have pin 20 (signal coming in from the double relay) connected internally, the pin is completely missing in the ECU connector (male) as well.
Here's a shot of the track side, I guess when your ignition pulses coming in (pin 1), are at above 900RPms, that's as good as the engine is running...

Eagle eyed viewers will probably notice the 'harnness' sticking out, I haven't got a suitable donor harness to cut up/use, so I'm making my own, should be interesting, more on that later.
I'm having issues figuring out where everything mounts, (now I realise I don't have pictures of my Aux air valve) I'm guessing the AAV mounts onto the thermo time switch's bracket, which is bolted to the engine near the pulley somehow.
If anyone has good clear pictures, also around the alternator mount position, I don't think the stock clamp will work here, the stand has 2 studs on either end, and no 'lip' for the 'normal' strap, please contact me, leave a comment or email (email address can be found on the left, under 'About Me').








For some weird reason my ECU doesn't seem to have pin 20 (signal coming in from the double relay) connected internally, the pin is completely missing in the ECU connector (male) as well.
Here's a shot of the track side, I guess when your ignition pulses coming in (pin 1), are at above 900RPms, that's as good as the engine is running...

Eagle eyed viewers will probably notice the 'harnness' sticking out, I haven't got a suitable donor harness to cut up/use, so I'm making my own, should be interesting, more on that later.
I'm having issues figuring out where everything mounts, (now I realise I don't have pictures of my Aux air valve) I'm guessing the AAV mounts onto the thermo time switch's bracket, which is bolted to the engine near the pulley somehow.
If anyone has good clear pictures, also around the alternator mount position, I don't think the stock clamp will work here, the stand has 2 studs on either end, and no 'lip' for the 'normal' strap, please contact me, leave a comment or email (email address can be found on the left, under 'About Me').
Sunday, March 1, 2009
3.875 R&P?
Been awhile since I've updated, busy with personal stuff. (Has to do with an 'arcade cab' I found at a dumpster, took me awhile to fix the broken monitor and sound.)
I managed to find a source of transaxles here locally. This is after a 300ishKM drive up to USJ in Malaysia to get one though.
Ah well, now I have 3 to work with. Including a AT code IRS that has a 3.875 R&P. Planning to transfer that over, and make a 3.88 swingaxle. Still undecided on what 4th gear ratio it'll be at, I'd think .89 would be too low, would need to rev the crap outta 3 before shifting into 4.
Now if it was a 5 speed....
BTW you sand rail guys really should check out this blog
http://www.turborail.blogspot.com
Turborail (Scott Smith), is tearing up his thing to build a new front and rear end. He's the guy who sent me some stuff the last time round. $$$ transmission he's got built... *drooooools*
I managed to find a source of transaxles here locally. This is after a 300ishKM drive up to USJ in Malaysia to get one though.
Ah well, now I have 3 to work with. Including a AT code IRS that has a 3.875 R&P. Planning to transfer that over, and make a 3.88 swingaxle. Still undecided on what 4th gear ratio it'll be at, I'd think .89 would be too low, would need to rev the crap outta 3 before shifting into 4.
Now if it was a 5 speed....
BTW you sand rail guys really should check out this blog
http://www.turborail.blogspot.com
Turborail (Scott Smith), is tearing up his thing to build a new front and rear end. He's the guy who sent me some stuff the last time round. $$$ transmission he's got built... *drooooools*
Rich running update 2
Ok, finally got around to tackling this problem again. Fitted a 122.5 main jet, she's now good.
Still no idea why it runs properly on this jet size, they are supposed to be running a 125... *trails off*
Ah well... will keep monitoring to see if it's too lean.
Still no idea why it runs properly on this jet size, they are supposed to be running a 125... *trails off*
Ah well... will keep monitoring to see if it's too lean.
Thursday, December 4, 2008
Rich running update
Ok a little update on why I think the engine is running richer then required. I've taken a picture of the spark plug. A little out of focus, macro photography is not my forte, need to get a macro lens quick...

I have the carb jetted currently this way at sea level(H30/31, I believe this is has a 25.5mm throat), also checked the float level and installed the right washer under inlet valve(1.5mm), fuel pressure is right at 2.8PSI...
Main Jet 125 (Most people are running 127.5 on 1600s, even at a step lower it's still running rich)
Idle Jet 55 (I can get the idle right, no smelling of gas out the exhaust at idle)
Air Correction 125 (Stock unit, not even sure I can get anything bigger/smaller to replace this with)
Power Jet 50 (Stock jet, I think I'll mess with it later after I've got the main jet right)
I originally thought maybe with the A/C on I might be sucking a larger vacuum then usual, thus leading to the rich running. Not so though, I tried running it without the A/C and still the same results.
I'm guessing because of the higher local temperatures (it's like 30deg C or 86deg F here on average), I can vapourise more fuel in the intake manifold, talk about free lunch hah, but this also means with the current fuel tank vent system (straight vent to atmosphere), the car will loose more fuel to evapouration...
Now to try a 122.5 or 120 main jet...

I have the carb jetted currently this way at sea level(H30/31, I believe this is has a 25.5mm throat), also checked the float level and installed the right washer under inlet valve(1.5mm), fuel pressure is right at 2.8PSI...
Main Jet 125 (Most people are running 127.5 on 1600s, even at a step lower it's still running rich)
Idle Jet 55 (I can get the idle right, no smelling of gas out the exhaust at idle)
Air Correction 125 (Stock unit, not even sure I can get anything bigger/smaller to replace this with)
Power Jet 50 (Stock jet, I think I'll mess with it later after I've got the main jet right)
I originally thought maybe with the A/C on I might be sucking a larger vacuum then usual, thus leading to the rich running. Not so though, I tried running it without the A/C and still the same results.
I'm guessing because of the higher local temperatures (it's like 30deg C or 86deg F here on average), I can vapourise more fuel in the intake manifold, talk about free lunch hah, but this also means with the current fuel tank vent system (straight vent to atmosphere), the car will loose more fuel to evapouration...
Now to try a 122.5 or 120 main jet...
Sunday, November 30, 2008
Summary
So this is what we've done.
Fixed transmission pop-out problems, this required a 4th gear set.
Fixed stumbling problems, still have a richness problem I'm trying to solve with the carb and A/C combination.
Had carburetor rebuilt.
New fuel pump.
New brake lines.
New fuel lines.
New rear wheel oil seals.
New rear axle boots.
New transmission mounts.
New shifter bushing.
New shift coupler bushings.
New manifold boots.
New pushrod seals.
Quite alot of new things eh? Really piles up when the Beetle can run with a few broken bits, but when a problem occurs, lotsa bits to fix (since you're there already).
Fixed transmission pop-out problems, this required a 4th gear set.
Fixed stumbling problems, still have a richness problem I'm trying to solve with the carb and A/C combination.
Had carburetor rebuilt.
New fuel pump.
New brake lines.
New fuel lines.
New rear wheel oil seals.
New rear axle boots.
New transmission mounts.
New shifter bushing.
New shift coupler bushings.
New manifold boots.
New pushrod seals.
Quite alot of new things eh? Really piles up when the Beetle can run with a few broken bits, but when a problem occurs, lotsa bits to fix (since you're there already).
Everything back together

After resting for a bit, actually an entire day. I got back to reinstalling the engine. Engine went in after 15mins, hah, getting good at this, have all the angles figured out to clear the alternator nut and intake manifold heat riser. Attached everything back on, A/C bracket, compressor etc.
Car was ready to be driven.
I don't have a driving license though, so only the other guys can drive the car, usually taking it around the block, this only tests 1st 2nd and 3rd gears, we did that a couple of times, it seemed fine. No more popout from 3rd gear.
It would be a good 3 days later, before the Beetle was driven 'properly' and 4th gear utilised. All good here.
Fixing transmission leaks
To try and fix transmission leaks. I've created a little checklist. This only pertains to swing-axle type transmissions, I don't have too much info on IRS, but I'd think they'd be very close, and possibly less prone to leakage.
1. Check and make sure the vent hole is open, the gasket that goes between the intermediate housing and nosecone might be blocking the vent hole. On our self-made gasket it was, I opened the hole and used a little sealant (Indian Head) on the gasket.
2. Make sure side cover O-rings are in place. Gasket on side cover was also self-made, a little sealant again here.
3. Axle tube retainer plates, this frequently go out of flat, from over-torquination (yes I know it's not a proper word), use a the ball end of a ball-peen hammer against it and smack it flat (use the ball-peen hammer like a drift pin). I tried my best here. Also coat every single layer of paper gasket used to set axle tube play with sealant. I also siliconed (here is the only place where silicone sealant should be used) the plate to the side cover.
4. Rubber boots, put them with the seam in the 2 or O'clock position, The clamps that came with our set sucks ass, it'd pull apart with enough torque. Put sealant between the seams before screwing them together, don't tighten too much, just enough to pull the 2 halfs together. You also want to position the clamp so that when you tighten, it pulls the halfs together.

5. Leaking at wheel bearing area. Make sure you have all the bits as shown in the above diagram, oil and install the O rings, after you have the inner spacer and wheel bearing in. Install the gasket with a little sealant onto the seal retainer. make sure the backing plate (even on the back side) is clean, if you have the vent hole, clear that out. Put the spacer into the seal, then onto the axle, trying to put the seal in while the spacer is on the axle frequently results in a torn seal (and leaks), because it didn't seat properly.
6. Input shaft seal, this is behind the throwout bearing. Change this if it's leaking. Might be a good idea to check if the clutch arm and the throwout bearing arm is in good shape, these can crack.
That's it, now your transmission should be pretty much leak free. If I've missed anything, do let me know so I can add it in.
1. Check and make sure the vent hole is open, the gasket that goes between the intermediate housing and nosecone might be blocking the vent hole. On our self-made gasket it was, I opened the hole and used a little sealant (Indian Head) on the gasket.
2. Make sure side cover O-rings are in place. Gasket on side cover was also self-made, a little sealant again here.
3. Axle tube retainer plates, this frequently go out of flat, from over-torquination (yes I know it's not a proper word), use a the ball end of a ball-peen hammer against it and smack it flat (use the ball-peen hammer like a drift pin). I tried my best here. Also coat every single layer of paper gasket used to set axle tube play with sealant. I also siliconed (here is the only place where silicone sealant should be used) the plate to the side cover.
4. Rubber boots, put them with the seam in the 2 or O'clock position, The clamps that came with our set sucks ass, it'd pull apart with enough torque. Put sealant between the seams before screwing them together, don't tighten too much, just enough to pull the 2 halfs together. You also want to position the clamp so that when you tighten, it pulls the halfs together.
5. Leaking at wheel bearing area. Make sure you have all the bits as shown in the above diagram, oil and install the O rings, after you have the inner spacer and wheel bearing in. Install the gasket with a little sealant onto the seal retainer. make sure the backing plate (even on the back side) is clean, if you have the vent hole, clear that out. Put the spacer into the seal, then onto the axle, trying to put the seal in while the spacer is on the axle frequently results in a torn seal (and leaks), because it didn't seat properly.
6. Input shaft seal, this is behind the throwout bearing. Change this if it's leaking. Might be a good idea to check if the clutch arm and the throwout bearing arm is in good shape, these can crack.
That's it, now your transmission should be pretty much leak free. If I've missed anything, do let me know so I can add it in.
After Jigging
Took down the entire transmission again, this makes it, I dunno, the 6th time? Lost count. Stuck the gear carrier in the jig, this was when everything became crystal clear.
The downshift grind problem was because the reverse had a whole lot of slop, and with me jiggling the reverse linkages, I can get reverse gear to hit the 1st-2nd slider while in 2nd gear.
I removed reverse, tightened the I bolt a little to try and reduce play. Adjusted 1st and 2nd slider (this was pretty close), adjusted 3rd and 4th slider (this was quite far off, I had set the slider to engage 4th too deep, and as a consequence wouldn't engage 3rd fully). Stuck reverse back in, adjusted that to engage fully with the 1st-2nd slider while in reverse, and not hit 2nd even with me jiggling the linkages on reverse while in 2nd (sounds really messy, but once you're in there you'll figure it out, I know I did).
The reverse gear system in the stock VW transaxle is really weak (at least it seems so to me), just not a very good design. I would like to thank Eric (http://www.shoptalkforums.com/profile.php?mode=viewprofile&u=5765) for responding to his email when I asked about the reverse gear adjustment, didn't know what to do at that time. His website at http://www.geocities.com/Baja/Dunes/9702/transtalk.html was also pretty helpful, they have some pictures too.
I spent about an hour jigging everything up. It was already past 2AM by the time I had the entire transmission back into the car. Muscle fatigue was also already setting in, so I left the engine on the stand and went home, best to have a helper, especially during the trying-to-balance-transmission-on-jackstand part.
The downshift grind problem was because the reverse had a whole lot of slop, and with me jiggling the reverse linkages, I can get reverse gear to hit the 1st-2nd slider while in 2nd gear.
I removed reverse, tightened the I bolt a little to try and reduce play. Adjusted 1st and 2nd slider (this was pretty close), adjusted 3rd and 4th slider (this was quite far off, I had set the slider to engage 4th too deep, and as a consequence wouldn't engage 3rd fully). Stuck reverse back in, adjusted that to engage fully with the 1st-2nd slider while in reverse, and not hit 2nd even with me jiggling the linkages on reverse while in 2nd (sounds really messy, but once you're in there you'll figure it out, I know I did).
The reverse gear system in the stock VW transaxle is really weak (at least it seems so to me), just not a very good design. I would like to thank Eric (http://www.shoptalkforums.com/profile.php?mode=viewprofile&u=5765) for responding to his email when I asked about the reverse gear adjustment, didn't know what to do at that time. His website at http://www.geocities.com/Baja/Dunes/9702/transtalk.html was also pretty helpful, they have some pictures too.
I spent about an hour jigging everything up. It was already past 2AM by the time I had the entire transmission back into the car. Muscle fatigue was also already setting in, so I left the engine on the stand and went home, best to have a helper, especially during the trying-to-balance-transmission-on-jackstand part.
Finally a jig
To try and save on shipping weight, the sender (Turborail) had the transmission cut up(just like the above diagram, if you want to try this), instead of sending me the entire case. Also got him to send us a shiny new adjustable type timing gun, this will let us time 0-60BTDC, with just the TDC mark. You just set whatever advance you want. Pull the trigger and see if it lines up with TDC. He also sent us some jets, I'm trying to re-jet the H30/31 better, bloody impossible to find jets here locally, or I haven't tried hard enough.

We made a handle thing to crank the gears over, don't have welding equipment, so we tapped a hole through and secured it to a bent stud, had some fun trying to drill the hard shaft... made a little handle with a piece of aluminium tubing. The coupling gear was jammed in place with a piece of paper, quite a firm friction fit, if the need arises, I can still reuse this coupler.

We also clearanced some of the splines along what was a transmission case, this would enable us to clamp the jig in a vice during use. I later attached 2 small pieces of foam so clamping wouldn't mar the case... Another picture below.

More transmision trouble
After having everything fitted, 4th gear now works fine, but during clutching (before enaging the clutch, i.e before letting foot off the clutch pedal) 3rd gear sometimes doesn't engage fully and pops out. At that time we still didn't have a transmission jig to adjust the shift forks properly. So the best was to eyeball it while everything is in, not very accurate since everything can still move around.
Before re-tearing down the transmission, the stop plate was re-adjusted to see if we can get 3rd to engage deeper, didn't quite work. During that time the little shift bushing in the tunnel was also replaced, this helped to remove alot of slop the shifter was experiencing, the shift coupler was pretty new and had no slop, so that was ok.
After replacing the shift bushing, shifting was now alot tighter, no more looking around for gears.
There was a new problem though, sometimes during downshifts from 3rd gear to 2nd, there'd be a little grind, almost like it was hitting reverse, but the stop plate is already well adjusted. At this point nothing more could be done without having a transmission jig, so we bit the bullet and got a cut up pinion nut type transaxle housing to use as a jig.
Before re-tearing down the transmission, the stop plate was re-adjusted to see if we can get 3rd to engage deeper, didn't quite work. During that time the little shift bushing in the tunnel was also replaced, this helped to remove alot of slop the shifter was experiencing, the shift coupler was pretty new and had no slop, so that was ok.
After replacing the shift bushing, shifting was now alot tighter, no more looking around for gears.
There was a new problem though, sometimes during downshifts from 3rd gear to 2nd, there'd be a little grind, almost like it was hitting reverse, but the stop plate is already well adjusted. At this point nothing more could be done without having a transmission jig, so we bit the bullet and got a cut up pinion nut type transaxle housing to use as a jig.
Pop-out, again...

After a few days working properly, the transmission decided to pop-out again. Was looking through some tranmission diagrams when it hit me, I had the spring washer that fits on the mainshaft bearing installed wrong. It's supposed to exert pressure against the snap ring and mainshaft bearing, n00b me (again).
Tore the transmission down again, getting really good at it too, can now get the engine out in about 1.5Hrs (sure, world record is less den 40 secs, but we've got A/C and everything in this sedan). Not fun, the other guys by now are pretty sick of taking the thing apart every few days already... can't blame them.
The pinion nut had somehow walked itself out, I guess I didn't tighten it enough, and never staked it in. After swapping and fitting the snap ring right, the pinion nut was fully staked in place.
Gears arrived, now to fit everything back
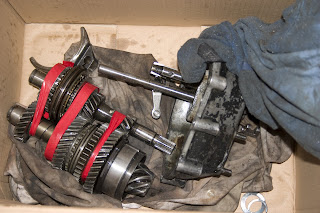
Gears came, had them fitted and the whole assembly was taped up, ready to be pressed in. You can see tack welds we've used to keep the snap ring in, don't want it coming off again, if needed the tack welds can be removed easily.
After it was assembled, everything seemed to work properly, no pop-out, all was good (or so I thought).
Saturday, November 29, 2008
While waiting for the gears to arrive
We cleaned the engine up, and disassembled the cylinder heads to change out the leaky pushrod tube seals. Rather uneventful (good thing), the studs were 8mm and already had case savers in, nothing stripped / pulled out. Heads came off with a little tapping around. The cylinder / head seal looked good, the inside of the cylinders still have some of the hone pattern.
Gave the heads a good scrubbing and a pressure wash. The tubes were taken off and the rust brushed off with a wire brush, a light coat of black paint was applied and the tubes given a little tug. I managed to cut myself a little with the lip of the pushrod tube, you want to be careful here. They are sharp.
Pre-oiled the seals and stuck them on the tubes, whole assembly was re-installed and heads torqued down. Replaced the gasket on the oil pump cover, was leaking. Also took off the alternator stand and redid the gasket. Found the oil deflector plate installed wrong, might be the cause of excessive oil leakage out the breather tube. You want it to be installed like this.

Fixed that and made new gaskets and reassembled everything. Gave it a clean again. Lotsa narly crap stuck onto the block.
The Beetle has had an A/C system installed. The mounting bracket screws into the block through one of the holes a stud sat originally between the 2 case halfs, we found the bolt a little too short to go through both halves, what a 1/2 assed job. Had to get a longer bolt that would hold both 1/2s together. The car now looked like this.

There were also cracks down the middle of the intake manifold boots, might be why we couldn't get the idle lower than 1K RPM with the bypass fully screwed in, replaced those also, looks like we'll be visiting carb retuning again.
The rear flexible brake lines also decided at this time to crap on us. The lines were broken where they were clamped off... changed them out for new ones, quite a chore with the gunk that had accumulated around the fittings, lotsa WD40 here.
Gave the heads a good scrubbing and a pressure wash. The tubes were taken off and the rust brushed off with a wire brush, a light coat of black paint was applied and the tubes given a little tug. I managed to cut myself a little with the lip of the pushrod tube, you want to be careful here. They are sharp.
Pre-oiled the seals and stuck them on the tubes, whole assembly was re-installed and heads torqued down. Replaced the gasket on the oil pump cover, was leaking. Also took off the alternator stand and redid the gasket. Found the oil deflector plate installed wrong, might be the cause of excessive oil leakage out the breather tube. You want it to be installed like this.

Fixed that and made new gaskets and reassembled everything. Gave it a clean again. Lotsa narly crap stuck onto the block.
The Beetle has had an A/C system installed. The mounting bracket screws into the block through one of the holes a stud sat originally between the 2 case halfs, we found the bolt a little too short to go through both halves, what a 1/2 assed job. Had to get a longer bolt that would hold both 1/2s together. The car now looked like this.

There were also cracks down the middle of the intake manifold boots, might be why we couldn't get the idle lower than 1K RPM with the bypass fully screwed in, replaced those also, looks like we'll be visiting carb retuning again.
The rear flexible brake lines also decided at this time to crap on us. The lines were broken where they were clamped off... changed them out for new ones, quite a chore with the gunk that had accumulated around the fittings, lotsa WD40 here.
Transmission Teardown X2
Ok, now that we've got most of the engine issues fixed, the transmision was looked at again. To do this, everything had to be disassembled again. Cock, I wish the transaxle had some kinda removable sump or something we can see everything from.
On disassembly, the transmission fluid looked really bad, it wasn't too long ago fresh fluid was stuck in, but it was now a milky grey colour, not good. Further teardown showed us what the problem was. Take a look at the picture below.

The 4th gear was broken, this was due to the snap ring falling off the end of the pinion shaft, we have the spring type of spacer between 3rd and 4th gear, the broken snapring caused the spring to push 4th gear out of mesh and chewed up the gear, this is also the fine toothed 4th gear, so I guess it couldn't stand the abuse, not likely the coarse toothed one would've lasted too long either.
A look on TheSamba's classifieds led me to this guy.
http://www.thesamba.com/vw/forum/profile.php?mode=viewprofile&u=47126
He has bunch of good used parts, and has a whole lot more experience with VW transaxles than all of us here put together, probably. Got a set of coarse toothed 4th gear from him.
This will also probably also solve our popout problem, because as I've found out, the popout is from the engagement teeth on the gear hub itself being worn (very little to do with detents as we've thought previously). The wear especially on the flanks, will cause the gear to push the slider out of engagement. The sliders themselves can be worn also, to check this, we had the entire assembly pressed out. The flank cut in the slider looks ok to my untrained eye, so we only got the gears.
On disassembly, the transmission fluid looked really bad, it wasn't too long ago fresh fluid was stuck in, but it was now a milky grey colour, not good. Further teardown showed us what the problem was. Take a look at the picture below.

The 4th gear was broken, this was due to the snap ring falling off the end of the pinion shaft, we have the spring type of spacer between 3rd and 4th gear, the broken snapring caused the spring to push 4th gear out of mesh and chewed up the gear, this is also the fine toothed 4th gear, so I guess it couldn't stand the abuse, not likely the coarse toothed one would've lasted too long either.
A look on TheSamba's classifieds led me to this guy.
http://www.thesamba.com/vw/forum/profile.php?mode=viewprofile&u=47126
He has bunch of good used parts, and has a whole lot more experience with VW transaxles than all of us here put together, probably. Got a set of coarse toothed 4th gear from him.
This will also probably also solve our popout problem, because as I've found out, the popout is from the engagement teeth on the gear hub itself being worn (very little to do with detents as we've thought previously). The wear especially on the flanks, will cause the gear to push the slider out of engagement. The sliders themselves can be worn also, to check this, we had the entire assembly pressed out. The flank cut in the slider looks ok to my untrained eye, so we only got the gears.
Timing light

Seeing as to how expensive, and impossible to get timing lights were in Singapore. I decided to make one out of little parts I had lying around. They are rather simple devices actually, a High-voltage power source for the Xenon flash tube, the flash tube itself, a little storage capacitor for the HV, and something to trigger the flash (the 3rd wire that goes around the flash tube, HV ionises the gas inside and causes the tube to fire).
The trigger itself can be the HV straight out from the Ignition coil, not the best solution, but it'll work. I wired a small black wire (you can see in the picture) to the trigger connection on the flash tube. The entire assembly was hot glued to a little plastic tray semiconductors are held in.
HV was produced using a small CCFL power supply. 12VDC in will result in almost 300VAC out on one leg. I used both phases on the board (board can power 2 CCFLs) to generate about 700VAC, used a couple of high-voltage rectifiers to convert that to DC the flash tube required, a smallish HV capacitor to store the charge.
Flash tube was from a disposable Kodax camera, had a couple of these some time ago when I was messing around with coil guns, I had gutted them for the storage capacitors to build a bank, I got these free from a photo developing store nearby, had to wait quite abit before they had some though.
Hooked up the timing light, and timed the 009 to 30deg BTDC at 4000RPM. It fell to 12deg BTDC at idle (about 1K RPM, we still had the high idle even-with-bypass-screw-totally-in syndrome). Engine was alot more responsive and powerful now with the timing 'right'. I'd recommend everyone who is using a 009 to time it using a timing light at max advance. There's no knowing where it'd fall to at idle. This seemingly high idle RPM advance makes me think either the distributor is worn, or someone messed with it before.
Stumbling AGAIN (A/C related)
Ok I lied about fixing the stumbling problem the last post. Actually everything would be fine, until you have the A/C turned on, and the idle speed would drop below 800RPMs, causing the engine to sputter and die out. I 1st tried adjusting the carb with the A/C on, not happenning, the fuel mixture screws were responding sluggish, bypass screw wouldn't bring the idle speed up even with it dangerously close to totally out. Pumping the accelerator would also cause the engine to cough and die, this was due to too big an accelerator pump output, so a quick adjustment fixed that.
PMed Keifernet over at TheSamba (http://www.thesamba.com/vw/forum/profile.php?mode=viewprofile&u=27&sid=d068d891b9191df5c9c889952e13e2c4), he has experience with Gilmore A/C units.
Although not recommended for normal carb tuning, he suggested I screw the fast idle screw in a turn to bring up the idle. I did that, and could now bring up the idle speed to the proper range (800-900RPMs).
So now what I do would be, adjust carb with A/C off as per normal. Turn on A/C, re-adjust carb with bypass and fast idle screw till I get the idle speed right, try to lean it out a little on the mixture screw.
I think the lowered RPMs due to the A/C compressor really screws with normal idle fuel metering. If I crack the throttle open using the fast idle screw to bring up RPMs, the mixture becomes seriously rich (smelling the tailpipe and getting stung by the exhaust will tell you that). I have yet to fix this problem totally, the spark plugs still read rich (black and sooty), if I don't use the A/C, and tune the carb as per normal it'd be fine (no sooty spark plugs).
Maybe I'll try tweaking the idle advance next.
If anyone has any tips on how to fix this problem, do let me know.
PMed Keifernet over at TheSamba (http://www.thesamba.com/vw/forum/profile.php?mode=viewprofile&u=27&sid=d068d891b9191df5c9c889952e13e2c4), he has experience with Gilmore A/C units.
Although not recommended for normal carb tuning, he suggested I screw the fast idle screw in a turn to bring up the idle. I did that, and could now bring up the idle speed to the proper range (800-900RPMs).
So now what I do would be, adjust carb with A/C off as per normal. Turn on A/C, re-adjust carb with bypass and fast idle screw till I get the idle speed right, try to lean it out a little on the mixture screw.
I think the lowered RPMs due to the A/C compressor really screws with normal idle fuel metering. If I crack the throttle open using the fast idle screw to bring up RPMs, the mixture becomes seriously rich (smelling the tailpipe and getting stung by the exhaust will tell you that). I have yet to fix this problem totally, the spark plugs still read rich (black and sooty), if I don't use the A/C, and tune the carb as per normal it'd be fine (no sooty spark plugs).
Maybe I'll try tweaking the idle advance next.
If anyone has any tips on how to fix this problem, do let me know.
Ok, but now hard to restart car when warm
Car was now running ok, except it took alot of cranking over to start her when warm, and there'd be a puff of black smoke out the tailpipe.
Did a quick check with the folks over at TheSamba, they mentioned that excessive fuel pressure could cause flooding because the fuel could seep past the float valve. Now was the time to get / build a proper fuel gauge.
Went down to the hardware store nearby, got myself a T fitting with suitable barbs on each end to fit the hoses we were using, got a gauge that read up to 15PSI fitted also. Tested the fuel pressure and found it to be at 7PSI, ok, now it's beginning to be clear why it'd flood. The recommened fuel pressure is no more than 3PSI.
The fuel inlet was also now loose from all this yanking and pulling on it, was spinning freely and leaking when there was fuel pressure. Apparrently this happens rather frequently as the inlet is just a pressed in fitting. There are 2 things we could do. 1. Pull out and knurl the fitting, then epoxy it back in. 2. Tap the top cover and install a threaded fitting (got the picture from on of the threads over at TheSamba).


We did the knurling and installed the fitting back in, you can also do the wire thing like in the above picture (got this from TheSamba), this will reduce the loading on the fitting and hopefully help it stay in place.
The mechanical pump was now back in stock, so we got that instead of messing around with a fuel pressure regulator. The base was packed with grease, and the pivot peened into place (they now have a nasty reputation for popping out and causing the pump not to work, staking them in helps alleviate the problem). Shimmed the base down with gaskets to keep the fuel pressure below 3PSI (says 2.8 on the gague), and all our hard start problems were gone.
But now there was a new problem, the dying problem was back... what the hell... took the fuel tank out and totally flushed it out. cleaned out the metal fuel line that runs in the tunnel, nothing. There was a lot of crud in the tank though, lotsa rust. We'd eventually have to POR-15 the tank I think. Fitted a fine paper element type filter and all was good, at least in the stumbling and dying out department.
Did a quick check with the folks over at TheSamba, they mentioned that excessive fuel pressure could cause flooding because the fuel could seep past the float valve. Now was the time to get / build a proper fuel gauge.
Went down to the hardware store nearby, got myself a T fitting with suitable barbs on each end to fit the hoses we were using, got a gauge that read up to 15PSI fitted also. Tested the fuel pressure and found it to be at 7PSI, ok, now it's beginning to be clear why it'd flood. The recommened fuel pressure is no more than 3PSI.
The fuel inlet was also now loose from all this yanking and pulling on it, was spinning freely and leaking when there was fuel pressure. Apparrently this happens rather frequently as the inlet is just a pressed in fitting. There are 2 things we could do. 1. Pull out and knurl the fitting, then epoxy it back in. 2. Tap the top cover and install a threaded fitting (got the picture from on of the threads over at TheSamba).


We did the knurling and installed the fitting back in, you can also do the wire thing like in the above picture (got this from TheSamba), this will reduce the loading on the fitting and hopefully help it stay in place.
The mechanical pump was now back in stock, so we got that instead of messing around with a fuel pressure regulator. The base was packed with grease, and the pivot peened into place (they now have a nasty reputation for popping out and causing the pump not to work, staking them in helps alleviate the problem). Shimmed the base down with gaskets to keep the fuel pressure below 3PSI (says 2.8 on the gague), and all our hard start problems were gone.
But now there was a new problem, the dying problem was back... what the hell... took the fuel tank out and totally flushed it out. cleaned out the metal fuel line that runs in the tunnel, nothing. There was a lot of crud in the tank though, lotsa rust. We'd eventually have to POR-15 the tank I think. Fitted a fine paper element type filter and all was good, at least in the stumbling and dying out department.
Stumbling X2

Ok, now we tried a full tune up, checked valve lash when cold, and re-adjusted as necessary, had to get new valve cover gaskets, old ones were disintegrating inside, PO had sealant all over to try and stop the leak, not fun trying to remove all of that, not cool also if the sealant came out and plugged up an oil passage inside the engine.
Next we static timed the distributor at 7.5 (eyeballed this, we have a degree pulley installed by the PO), didn't have a timing light, so best we could do at that moment (previously we just marked the base of the distributor and always re-installed it so the markings lined up, no idea what it was timed at).
Also got a rebuild kit, and cleaned out the entire carb and changed the diaphragms and O-ring seals around the mixture and bypass screws, new inlet valve as well.
New fuel hoses were also installed. Everything from under the fuel tank to the rear was now new.

We then also tested the mechanical fuel pump, no fuel pressure gauge that time, so we just stuck the outlet into a clear bottle and cranked the engine over to see if there was flow. The 1st time we did this, a little stream came out. Went off for a smoke / water break before assembling everything back.
When everyone was back, we decided to try the pump again, the 2nd time, no matter how hard we cranked it over, no fuel came out. COCK, bloody thing was intermittent. A quick check was done with the parts store, no fuel pump. So we decided to get an electric pump. We manage to source a pump locally, it was a solenoid type that made a tic-tic-tic sound everytime it operated, hooked it all up and the car performed ok for the 1st time in many days.
What is causing all that stumbling

To try and fix the stumbling problem. We 1st tried to re-tune/adjust the carburetor. The carb on the vehicle was an aftermarket H30/31 and the distributor was a German made Bosch centrifugal advance 009 (Yeah not the best distributor, I know).
Tweaking the idle speed with the bypass screw (the large brass screw) was impossible, this tells us we had some kinda crazy vacuum/intake leak. After a little digging, it was found that the carb base wasn't tightened tight, and the gaskets had all disintergrated. Made a couple of gaskets using some gasket paper, and retightened the carb and it's adapter (adapter is needed to fit the H30/31 on the dual port manifold). Seemed to help it a little, now the idle could be adjusted, but even with the screw in all the way, she was idling high (1k RPMs). Not too bothered with it at that time, we decided to leave it as is for the moment, and went for a test drive.
Driving it out, it seemed fine for a couple of mins, then the stumbling began all over again. The vehicle would loose power, and even with the throttle floored, never pick up speed, and eventually stall.
Stalled around the bend in front of a police station LOL (For Singaporean readers this was I believe Tanglin Police Divisional Headquarters), a cop came out and asked if we needed help, told him we didn't yet, continued pushing the car back. Stopped at a bus-stop nearby, for a little break. We tried starting her, still wouldn't start, pumped the throttle a couple of times, and she started. Goosed the car slowly back, not a fun experience, had woobly legs after.
So what is causing the popout? (And our n00bness)
Now that we have the gear train out, what was causing gears to popout? Having no clue at that time, we kinda poked and looked around, then decided maybe it was the detent mechanism loosening up (the shift rails were now easily activated). So we went and got new detent plugs and springs.
Installed new springs and plugged it back up. We put markings on the shift rail and re-assembled the shift forks back to their original positions, no jig at that time, had no idea one existed/was needed. Stupid n00b us.
Also installed new mounts, 1 front and 2 rear ones.
Buttoned up the transmission and reinstalled everything. Time for the moment of truth, shifted into 4th, wow, it now stays in there, waited.... POP!... COCK!
The car at this time, was also running poorly, it wouldn't hold a steady idle and would randomly die out while running on the road, had to push the car around quite a few times, we thought we must've disturbed or broke something during the period it wasn't running. So we got around to fixing those issues 1st before attending to the transmission again (transmission was pretty much back to square 1, except it would now take a little longer to popout, if you gently goosed it it'll stay in).
Installed new springs and plugged it back up. We put markings on the shift rail and re-assembled the shift forks back to their original positions, no jig at that time, had no idea one existed/was needed. Stupid n00b us.
Also installed new mounts, 1 front and 2 rear ones.
Buttoned up the transmission and reinstalled everything. Time for the moment of truth, shifted into 4th, wow, it now stays in there, waited.... POP!... COCK!
The car at this time, was also running poorly, it wouldn't hold a steady idle and would randomly die out while running on the road, had to push the car around quite a few times, we thought we must've disturbed or broke something during the period it wasn't running. So we got around to fixing those issues 1st before attending to the transmission again (transmission was pretty much back to square 1, except it would now take a little longer to popout, if you gently goosed it it'll stay in).
Disassembling the Transmission
Ok, here's the part I think most people would be interested in. We'll start with the easy stuff 1st.
Make sure you've got cloth/newspaper/cardboard lined on the work area, as this is about to get really messy with the old lube.
Remove the axle tube, either by using a puller or by wacking the end of it out. You want to save the paper shims that go between the sidecover and axle tube plate, at least measure the thickness and write it down somewhere, these determine the amount of play the tube will have, we only found out about this later during assembly.
Take off the plastic flower thing that sits between the side cover and axle tube if you have it, I think some years they aren't present.
Undo the nuts that hold the shift hosing/nosecone on. Check the hockey stick, make sure it isn't cracked/broken. Check the seal at the end to make sure it isn't leaky.
Next we need to removed the side covers, do the side where the starter mounts on 1st (number 9). Using a drift pin or blunt chisel, slowly tap against tabs on the circumference to break the side cover loose (make sure you've got all the nuts and washers out 1st, I used a pan with a magnetic base to hold everthing). Try not to damage anything, the key is to tap slowly against the tabs.
Afterwhich you can use a mallet and drive the differential (still with axles attacked, you can detach them by removed the circlips that hold them in) out together with the side cover on the other side, place the diff assembly and sidecovers somewhere safe. There was nothing wrong with our diff, so we didn't tear it down any further.
Now removed the nuts holding the intermediate housing (number 5, sorry I don't have a picture, hands were really greasy)
We then move to the area left when the diff was removed. Undo the spring clip holding the coupler in, remove the coupler and unscrew the inputshaft, make sure you don't loose the little stud.
Now the pinion bolts or the large nut has to be removed, the bolts are pretty easy, if you have the large nut, you can get the $$$ nut removal tool, or like me use a blunt chisel and tap it loose, then slowly with gloved hands remove it.
Here is where we got stuck, with everything removed we still couldn't pull the gear assembly out of the case, after a little poking, turns out the pinion has to be pushed out, you can do 3 things here. 1. Get the leverage tool, Longenterprises has it I believe. 2. Smack it out with a mallet. 3. Use a screw type jack, with a little piece of wood against the case and pinion, and slowly 'jack' the pinion, which will push the gear assy out and away from the case. There, you now have everything out. (Mostly)
Removing the Transmission

Removing the transmission was alot more involved than removing the engine itself. The drums had to be removed, the brake lines crimped off and the bearing retainer and backing plate removed.
Next bolts holding the axle tube to the spring plate and rear shocks were removed. This was done after a chisel was used to mark the position of the axle tube relative to the notch already on the spring plate.
We had a hard time trying to remove the axle tube with the transmission in place, so we left it hanging and removed it with a 3 jawed puller after taking out the whole transmission.
A standard jack was used to lower the transmission after the gear lube was drained out. It was pretty yucky, not too sure how many years has passed since the last change. Next would be trying to disassemble the transmission.
Removing the engine

Removing the engine was quick, we have an adjustable transmission jack that we use, this makes tilting operations alot easier, sure beats trying to balance the engine on a small jack.
The clutch and pressure plate were pulled, and found to be still in good condition, since we already had the engine out already, the gland-nut was replaced. (the gland nut holds the pilot bearing the input shaft of the tranmission rides in, with it worn all sorts of shifting / grinding problems might occur)
The distributor was given a good clean-up and everything was set aside, next was the transmission.
How it all started

Having lotsa spare time. We (me and the mechs working at the workshop) one day decided to take apart the Beetle to try and fix the 4th gear pop-out problem it had.
Other than that it was at that point of time considered running rather well (no stumbling/dying out, good brakes etc). Without much knowledge at that moment about what could actually be wrong, we dived in.
This blog was actually started after I had everything sorted out (explains the weird post dates), I guess it's a good place for others to get more information if they want to attempt anything like this, I've probably already made all the silly mistakes. I'll also probably laugh at myself later while reading it over again.
Subscribe to:
Posts (Atom)